涂装施工中钢板预处理的作用
发布时间:2014.07.11 点击数:6579
一、钢板预处理线的作用
为了充分发挥涂料对底材的保护、装饰作用,底材的表面处理质量直接影响着涂装工程质量。所以钢板预处理线在涂装施工中作用是非常大的。
实践证明,大部分的深层缺陷都来自于不良的表面处理,任何涂料在处理不良表面上都无法发挥其最佳性能,在氧化皮、锈蚀、油污表面涂漆,无论是时间上还是金钱上,都是极大的浪费,高等级的表面处理质量将会延长涂料的使用寿命。
在涂装前钢板的表面处理分两个阶段:
钢板进厂后,在加工以前对钢材的原材料先进行处理,除去表面的氧化皮和锈蚀,达到除锈标准后涂上临时保护车间底漆,以确保钢材在加工制造构件过程中不会再继续腐蚀,这一阶段的钢板处理我们称之为钢材的表面预处理,其优点是施工方便、保证涂装质量、节约人力财力、缩短后期涂装的施工周期。
另一阶段处理则是在钢材加工成工件后合拢成整体时,要进行涂装所作的钢材表面处理,称之为"二次除锈",但一般不采纳此种方法。
二、钢板抛丸预处理流水线过程
在国内造船、集装箱、大型机械行业中,一般用钢板预处理线设备上的抛丸机抛丸的方法进行磨料处理、喷射磨料处理和酸洗处理三种方式。其中要获得高效率、高质量的自动流水作业,目前还只有抛丸处理方式。
抛丸处理是利用路面抛丸机和叶轮在高速旋转时所产生的离心力将弹丸丸料(钢丸、钢丝段、棱角钢砂等)以很高的速度射向待处理的钢材表面,产生打击和磨削作用,除去钢表面氧化皮和锈,让钢铁表面露出金属本色并且呈现一定的粗糙度,以利于涂料的粘附。
抛丸预处理流水线,总体上有两种类型:一是钢板预处理流水线,另一种则是型钢预处理流水线,两者工作原理是一致的,现造船厂、集装箱、大型港机厂采用第一种方法,一般性钢结构厂采用第二种方法,两种方法目的一致都是为了保证涂装质量。
钢板抛丸预处理流水线的工艺流程图:
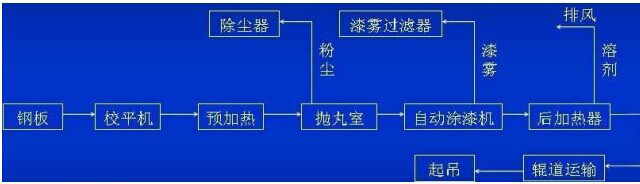
(一)钢板校平
钢板运输过程中经过长期的堆放后,会产生变形,在工件制作中,影响加工精度,所以应对钢板进行校平处理。经过校平可以将钢板表面氧化皮松散部分脱落,对后道抛丸有很大好处,同时校平机能力各有不同一般5mm—30mm为宜。
另外也有把钢板校平机放在流水线后面,这对车间底漆的性能是一种考验。
(二)钢板运输
钢板上料后,各工序的传送由辊道完成。
辊道通常为圆柱形,两端有轴承座,辊道间距为500~750mm,在喷涂工作完成之后,为了防止与辊道接触一面的油漆受到破坏,对辊道的结构形式有特殊的要求,所以一般辊道与钢板接触部位不会产生大面积的车间底漆损伤,受到影响很小。
为了保证钢板在抛丸处理时不变形,抛丸机内辊道间距不小于500mm。
(三)预热
预热是为了抛丸前装饰钢板升温,除去表面水分、部分油污,使钢板升温达到喷漆后的干燥。
一般预热与民同乐电热丝加热、中频感应加热、液化石油加热和水加热等。
不论采用何种方式加热,均应使钢板温度保持在40℃左右,温度太低,不利于除去水份、油污,后道喷涂底漆的干燥,温度太高,多耗能量,造成油漆干燥过程中起泡的弊端。
(四)抛丸器
抛丸器由叶轮、护罩、定向套、分丸轮、轴承座及电动机组成,叶轮由电动机带动调整旋转(2200~260转/min)产生强大的离心力,磨料经进尺管吸入分丸轮中时,在离心力作用下向叶片长度方向以加速运动60~8米/秒的速度抛出,抛出的磨料成扇形流速将钢板表面氧化皮和锈蚀除去。
1 一般抛头4个~16个不等,抛头离钢板间距大约为300~400mm,并且要调整工件与抛头的角度、方向,控制好每个抛头量。
2 6mm以下钢板扁钢、型钢不适合钢板预处理,因太薄会变形。
3 控制好抛丸的速度。
4 选好合适的抛丸钢丸及棱角砂。
(五)喷漆
经抛丸处理后的钢表面需要立即喷涂车间底漆。
1 喷涂设备为国产长江9℃高压无气喷漆泵,压力比为1:32
2 喷嘴一般为19~250、19~400、17~350、17~400左右。
3 喷涂车间底漆时搅拌机不停地缓慢搅拌直至用完为止。
4 喷枪与钢板之间距离通常为300mm左右,下喷枪距离应略小于上喷枪的距离。
5 油漆喷覆为50%。
(六)烘干
喷漆后应进入烘干炉内,促使漆膜快速干燥以利于迅速搬运、堆放。
(七)磨料
喷砂使用的磨料可以分为两种:金属质和非金属质(矿物质)或矿渣。金属质如钢丸、钢渣及钢丝段等,它们多为一次性使用的磨料,但抛丸磨料有铁丸、钢丸、棱角砂和钢丝段等,为理想磨料并且是混用磨料,直径大约0.8~1.2mm为宜。(粗糙度为40~75mm)
(八)粗糙度
抛丸后钢表面的粗糙度指抛丸时钢砂打击在钢板上残留痕迹的深度,粗糙度过小,钢板表面平滑,涂层附着力差,粗糙度大,油漆不能覆盖住粗糙度的波峰,易形成点蚀,而且会增加油漆消耗量,一般无机硅酸锌车间底漆的粗糙为40~75μm,必须要控制好以下方面:
1 保持好叶轮转速,不让钢砂抛射速度过快过慢,并且要控制钢砂的抛丸量。
2 调整好钢丸和棱角砂的配比。
3 钢尺和棱角砂直径、磨料颗粒度大小。
4 控制好抛头与钢板角度和距离。
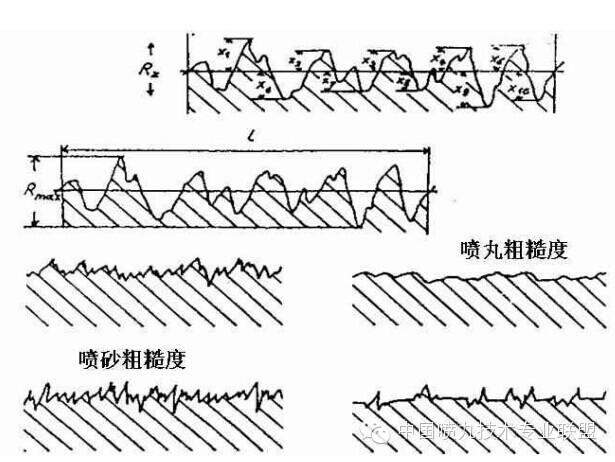
(九)预处理车间底漆干膜测量方法
车间底漆施工在喷砂处理到ISO sa2.5级钢板上,粗糙度达到R240—75微米,而车间底漆本身的百度要求一般在15—20微米,所以不能直接在钢板上测量膜厚,标准的测试方法为:
1 喷砂后把光滑板用胶带固定在钢板上,通常放置三块(如图示)
2 对电子式测厚仪先进行校正。
3 喷漆干燥后取下试板进行测量。
4 通常按喷砂后要达到规定的干膜百度在光滑试板上测量要高于规定值(见表)
5 对放置试板的位置要立即补涂。
粗糙度与漆膜百度的关系
光滑试板 |
R2=40微米 |
R2=70微米 |
20微米 |
15 |
12 |
25微米 |
20 |
15 |
将抹布摩擦50次来回:抹布无锌粉表示已固化;后面上锌粉很多表示没有固化。
处理方法:进一步固化和重新喷砂。
(十)无机硅酸锌车间底漆性能介绍 Interplate 317(NQA311/NQA317)
良好的焊接性和切割性
1 良好的干性(在23℃时5分钟干燥)
2 良好的耐溶剂性,能与各种防锈漆配套。
3 防腐为3个月至6个月。
4 良好的耐热性,减小受热破坏。
5 良好的机加工性。
6 良好的低毒性。(有卫生指标)
7 良好的耐电位性,适合船舶的阴极保护。
— 焊缝的成型和内在质量不受影响
— 焊缝的机械强度不受影响
— 切割的速度不受影响
— 切割的光洁度不受影响
同时选用的车间底漆必须获得船级社的认可。
车间底漆的特点:含锌,具有电化学保护作用,但有锌盐产生,热加工时,锌蒸汔产生小,适用于阴极保护,而高温(400~600℃),热影响区较小,膜厚为20-25微米时,防锈期一般为九个月。